Boiler room automatic control system
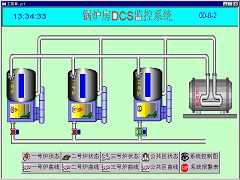
Product description:
; boiler room automatic control system
I. system overview
The automatic control system of a small boiler room, using SIEMENS S7, 300DP PLC, and the host computer to complete the real-time measurement and control tasks, select the appropriate amount of Party A according to the requirement of monitoring (temperature, pressure and flow rate) and the design of measurement and control software for special packages, 4 boilers for district heating system is composed of automatic control.
Boiler automatic control system through the detection of the outdoor temperature and indoor temperature remote real-time online, according to set parameters, heating room temperature standard, complete heat exchanger 3 valve opening and closing and opening, circulating pump start and stop the speed of residential buildings, 2 valve opening control, tracking and adjusting the heating temperature stability in the setting value. And heating system to achieve the expected high efficiency and energy saving operation.
The system can set the operating experience of the heating system on the computer, and adjust the operation mode of the system. In the completion of automatic adjustment, alarm and other functions at the same time, to achieve data display, management, operation, reporting, printing and many other functions. Through remote network communication port, data exchange can be carried out with the production scheduling management control system of the head office of the first party.
The automatic control system is manufactured strictly according to the industrial standard. It has high automation, good adaptability and good reliability. It is suitable for industrial application environment.
Two. Structure of automatic control system for boiler room
The control system consists of field instrument and actuator, S7-300DP CPU host and distributed I/O, system control part, upper monitoring computer and so on.
The field instrument mainly completes the field signal measurement, and the analog output is 4~20mA signal and digital I/O signal output.
PLC control system part, mainly completes the scene signal processing, the movement control algorithm and the output control signal and so on function.
Monitoring computer mainly completes system monitoring, control data insertion, system response record and so on. Man-machine interface, which is the interface of all Chinese characters.
The field instrument is installed at the appropriate measured point. The distribution of I/O control cabinet is installed in the vicinity of each boiler, and then aggregated through the PROFIBUS bus to the control room, and then to connect with computer, the realization of communication; monitoring computer in the control room, optional appropriate printer, optional hot standby computer.
Automatic control system diagram of boiler room
2. Monitor the computer "monitor interface" icon
The diagram is the "monitoring interface" of other automatic control systems. It is specially designed according to the actual situation.
3 、 monitor the computer "boiler real-time temperature trend map" icon
The monitoring machine can automatically record and save the temperature variation trend of the boiler outlet for a certain period of time, and can also increase the trend of other detected quantities.
4, monitor the computer system alarm table Icon
Three 、 boiler room automatic control system control method
the automatic control of the system, there are 3 main valve, 2 way valve, circulating water pump, flue gas discharge and other 4 automatic adjustment parts, the specific settings are as follows:
1; boiler room automatic control system; automatic regulation loop processing
1) automatic regulation loop setting
The water temperature automatic tracking and regulating loop is a lag regulation system and adopts cascade regulation loop. The main loop is the temperature loop, the hysteresis loop is PID1, the secondary loop is the flow loop, and the fast loop is PID2. The other loop is the pressure loop, and the fast loop is PID3. Flue gas emission adjustment circuit, pending.
2) automatic control circuit block diagram
3) automatic adjustment method of control system
The outlet temperature of heating furnace is affected by many factors. Real time on-line monitoring is required to achieve high efficiency.
Automatic adjustment method (a)
On the basis of circulating water flow and system pressure stability, the system automatically tracks and controls the household temperature, and makes the outlet temperature stable to the set point.
B) automatic adjustment process
System work, manual and automatic 2 modes of work.
Manual mode, the PID is in manual mode, does not participate in the adjustment, only follow the data, you can manually adjust the temperature.
Automatic mode, the PID is in automatic mode, and the automatic tracking is completed based on the set expected value. When the temperature is changed artificially, the setting temperature is gradually approached in an automatic tracking manner. At a given time (can be set by default 1).0 hours) unable to track the setting temperature. Automatically alert the attendant to see if other parts need to be adjusted.
Manual / automatic switching is usually performed when the system is near steady state, and the system will be switched without disturbance. In non steady state switching, the system will operate automatically.
2. Automatic alarm system for boiler room automatic control system
in order to ensure the normal operation of the boiler set the alarm signal, the alarm threshold according to production needs, set up, change, and by the main controller memory and implementation. The alarm program is called by different alarm reasons.
3, alarm signal table.
4 monitoring and control signal list
Serial number
function
No.
Model specification
Number
control point
control signal
01
Temperature transmitter
T for 1 and T back 1,
Two
AI
4~20mA
T for 2 and T back 2,
Two
T outdoor 1, T outdoor 2,
Two
02
Pressure transmitter
P for 1 and P back 1,
Two
AI
4~20mA
P for 2 and P back 2
Two
03
Flow transducer
L for 1 and L for 2,
Two
AI
4~20mA
L back 1 and L back 2,
Two
Four 、 function and characteristics of automatic control system for boiler room
system function
The main working interface, manually set the flow, change the temperature, automatically tracking the setting temperature
Trend chart, see temperature, flow, pressure change process
The trend chart enlargement curve is used to analyze the work of PID and optimize the control parameters
Data browsing to look at the historical data of 300 monitored signals that are regularly collected
Parameter settings, set PID, instrument range, alarm limit and other parameters
Alarm table, check alarm point record
System testing to view monitored signals AI, AO, DI, DO, real-time data
users log in to distinguish the privileges of different users
System help, read brief instructions for use
system characteristics
The system adopts real-time on-line measuring method with accurate measurement and high accuracy
The system can switch manually / automatically without disturbance, and realize manual adjustment of temperature and automatic tracking
The system adopts cascade PID adjustment algorithm, which improves the control accuracy and stability
The system control parameters and functional parameters can be adjusted at any time to adapt to different application environments
The system automatically generates the running curve and records the running data regularly, so it is convenient to analyze the change of crude oil temperature
System real-time display temperature, flow, pressure and other control data
The system is man-machine interface with full Chinese characters, which is intuitive and convenient to use
The system has many alarm functions such as temperature, flow, pressure, time out and so on
The system supports many communication modes, and can be used in many systems
The system has watchdog function
System control data power-off protection, can be stored for 10 years
The system's measurement and control components are completely isolated from the external instrument or equipment so as to avoid external interference
The main controller of the system adopts excellent industrial products, which is advanced in performance, reasonable in structure, excellent in temperature characteristics, and can work in harsh environment
Five. Main performance indexes of automatic control system for boiler room
Temperature regulation range party a set
Temperature control accuracy £ 5
Temperature overshoot ; £ 5
Temperature stability time according to heating system test
Display accuracy ;  
Measurement accuracy; + 0.1%
Output accuracy + 0.1%
Instrument power supply ; 24VDC/1A + 10%
Whole machine power supply ; 220VAC/3A + 10%
Operating temperature -100C ~ 700C